In AHNAKOT will Moving beyond tradition to Industry 4.0 with state-of-the-art approaches. Driving the circular economy, non-linear production, integrated supply chains and research-based innovation. A cleaner, smarter and world-defining business landscape.
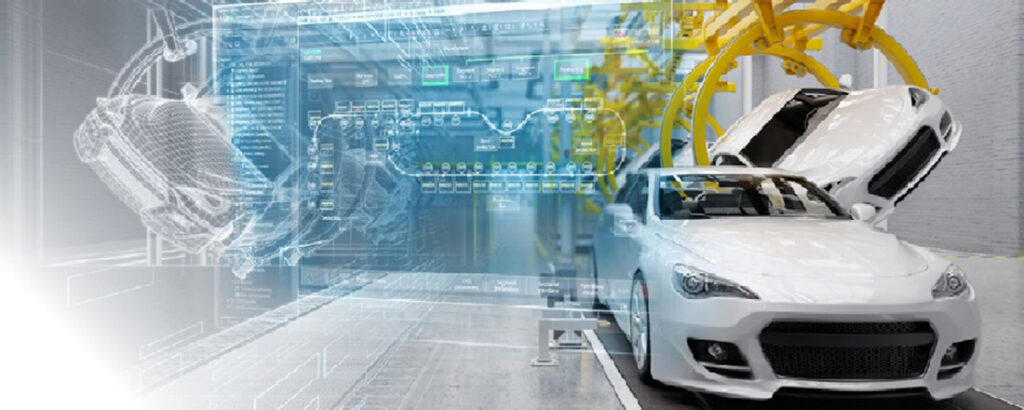
Industry is facing major challenges: Customers are demanding new, individual, high-quality and nevertheless inexpensive products within shorter and shorter periods of time. At the same time goods have to be manufactured from increasingly scarce resources, as sustainably as possible. In order to meet these requirements, research and business are turning to the digitalization of manufacturing, in which the real and virtual worlds converge in an Internet of things, services and data.
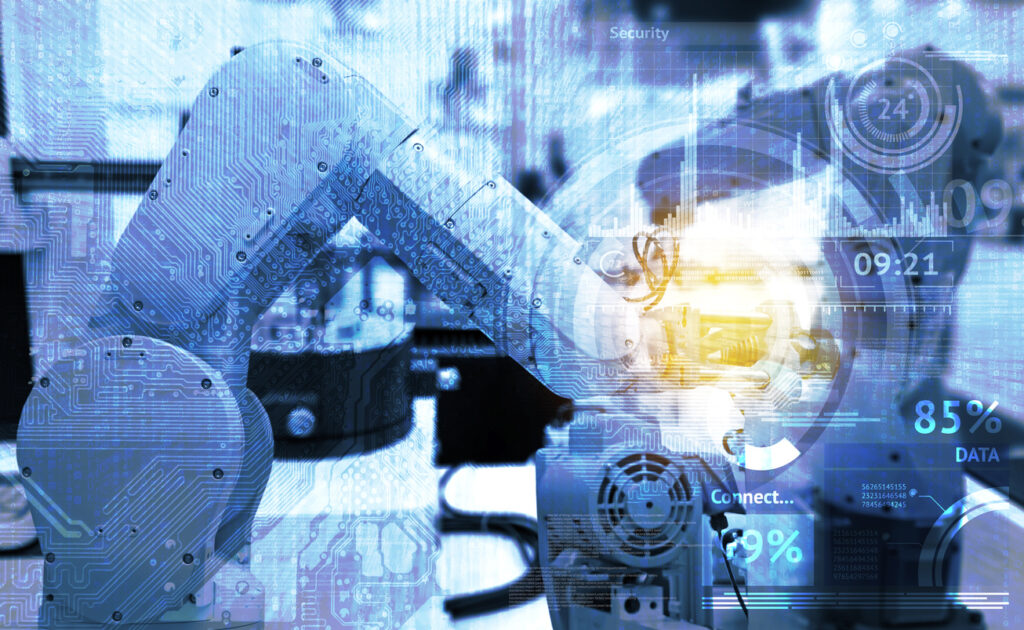
Here machines, workpieces, means of transport and goods are equipped with embedded systems, i.e. tiny computers, sensors and actuators and are connected with one another. This paves the way for the next jump in manufacturing, Industry 4.0.
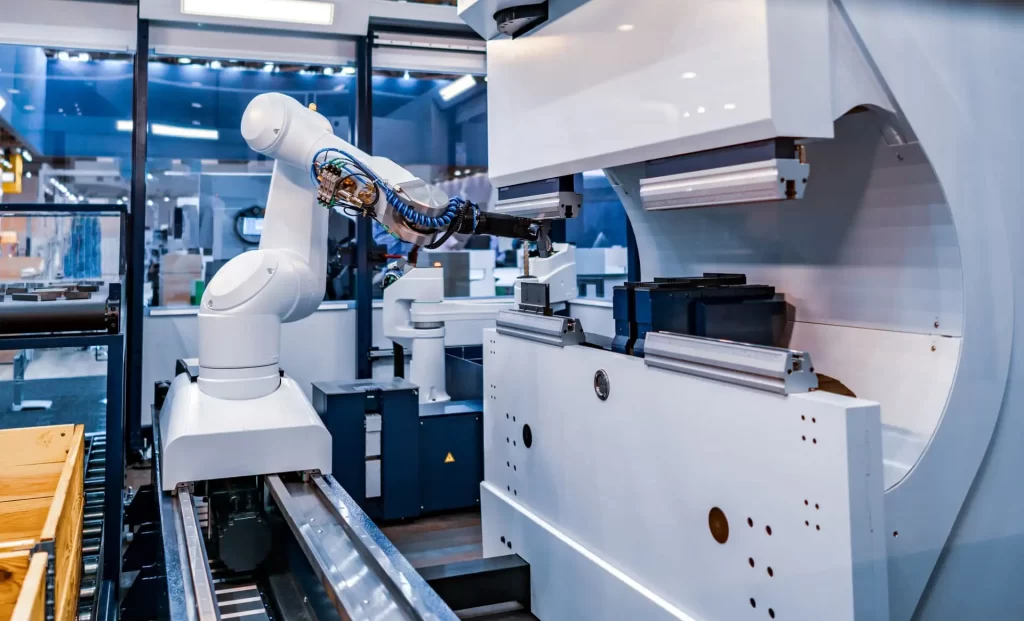
The Digital Transformation of Industry
In AHNAKOT all machines, from the milling machine to the welding robot, will be networked with one another. And every workpiece will have its own embedded system, storing various pieces of information for example on the customer, the workpiece’s desired configuration and its destination. It will be possible to uniquely identify and localize raw parts. Not only will they know the processing steps necessary, these parts will also be networked with the production machines and will be able to communicate with one another to decide exactly when they are to undergo which production step. In AHNAKOT the entire line will no longer stop when a given station fails. Instead, workpieces and machines will work together to replan the processing sequence. The result is a “self-organizing” adaptive manufacturing process that no longer requires constant human intervention, while remaining under human control.
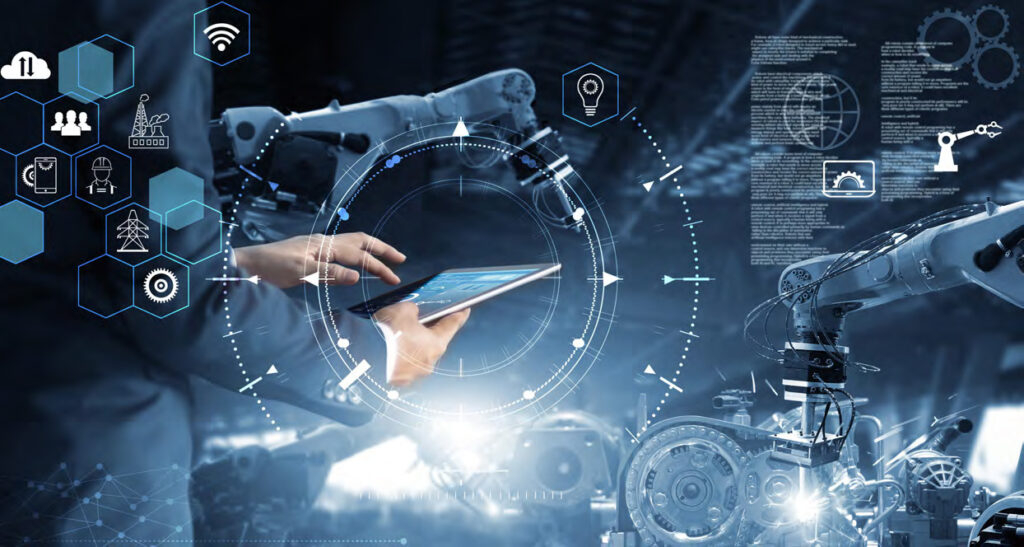
In order for smart production to run smoothly, the humans and robots involved have to continuously report exactly what they are doing and for example how long parts subject to wear have until they fail. Everything taking place in the real factory will be represented in parallel in the virtual factory. Experts refer to this connection of the real and virtual worlds as a “cyber-physical system”(CPS). The economy is hoping for several advantages from the digital transformation of industry: The flexible factory of the future will make it possible to manufacture according to customer preferences and make production changes ranging up to the integration of new machines at any time without substantial effort. Machine utilization levels will be higher, the consumption of resources will drop, and there will be fewer rejects.

“Plant Adapter” Simplifies Communication Interfaces
Another important prerequisite for smart factories is the ability of machines to communicate with one another, with higher-level IT systems and even with the workpieces and production workers. However, the networking of existing facilities quickly reaches its limits, since machines from different vendors usually communicate using different data interfaces and protocols. One solution here is the “Plant Adapter”, an industrial data gateway developed by experts at the Fraunhofer Institute for Machine Tools and Forming Technology IWU in Chemnitz, Germany. A combination of hardware and software, the “Plant Adapter” is a solution for universal connection of machines and other components in manufacturing and production infrastructure. It collects a wide variety of production and machine information and prepares it for reading and processing on a platform-independent basis. “Data as a resource is constantly growing in importance. New methods and solutions are needed in order to increase the value of data in the manufacturing environment even further.”
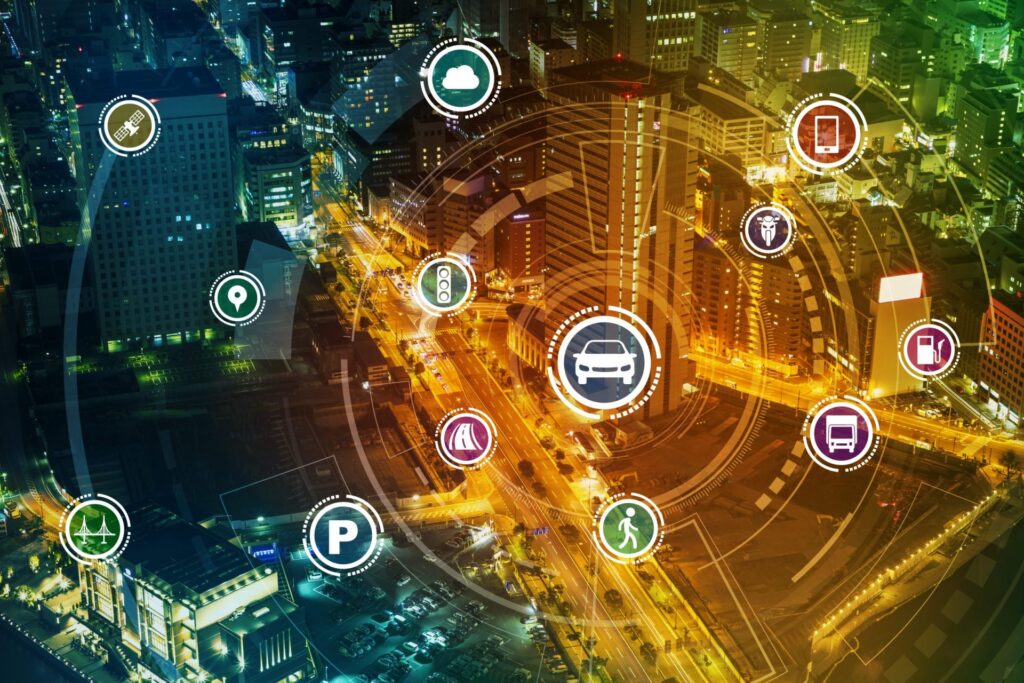
Flexibly Convertible Factories
Shorter innovation cycles and individual products call for not only flexible production, but also convertible factories that can be quickly reequipped to manufacture new articles. “One of the challenges faced by Industry 4.0 IT architecture is adapting to changes, whether resulting from integration of new facilities or processes in the system or from changes in existing production systems, for example because a particular new product variant is to be produced.
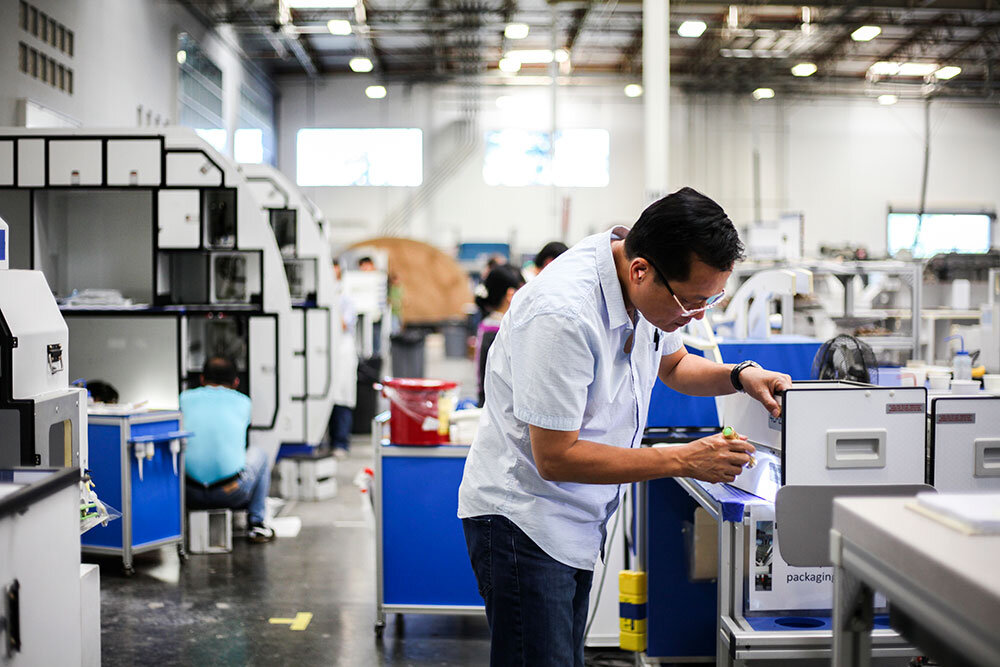
Humans Wanted
In order for humans to be able to work properly in the smart factory of the future, new human-machine interfaces will be needed: Smart Devices. These mobile devices are equipped with various sensors and connected on a wireless basis. The Coaster®, only about the size of a beverage coaster, can be used in logistics. The device not only features a camera and a display, it can also communicate with other machines via various interfaces. The exact function the Coaster® performs is decided by the applications that run on it. Thus for example the machine app shows production machine energy consumption, run-time and machine error messages. In order to seamlessly integrate the worker in production information processes, the Fraunhofer Institute for Production Technology IPT is taking a user-centered point of view in the design of its “oculavis” software platform. “oculavis” can be used together with apps for terminal devices such as Smart Glasses or tablets to optimally control the factory’s information flow to and from the worker. For example, at Robert Bosch Elektronika Kft. in Hungary, “oculavis” uses Smart Glasses to make it possible for even untrained employees to conduct complex installation processes within a very short period of time. Starting in May a spin-off partnership with Fraunhofer IPT will enhance and commercialize “oculavis”.
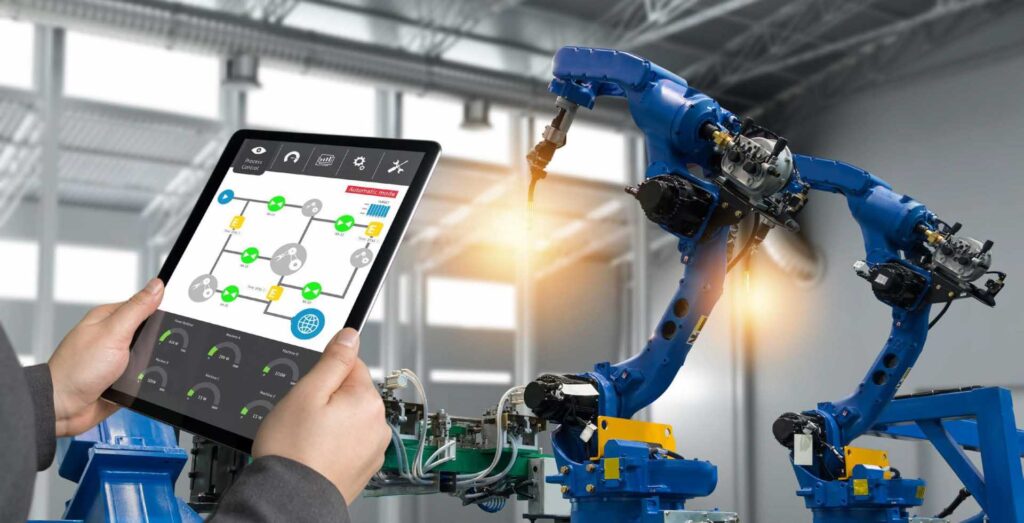